Fresh from redelivering the second ACJ TwoTwenty cabin, Comlux Completion explains how outfitting times can get progressively shorter
The ACJ TwoTwenty programme was announced by Airbus Corporate Jets (ACJ) in 2020, with the aircraft marketed as an ‘extra-large bizjet’. Uniquely among ACJ’s line-up, the ACJ TwoTwenty interior is selected by customers using a flexible cabin catalogue.
Comlux Completion in Indianapolis, Indiana, was chosen as ACJ’s exclusive partner to outfit the first 15 cabins. It inducted the first in January 2022 and announced its handover in May 2023. Comlux announced the second redelivery in February 2024, and shares the completion was just above the 12-month mark. The company has the goal to reduce the lead time with each aircraft.
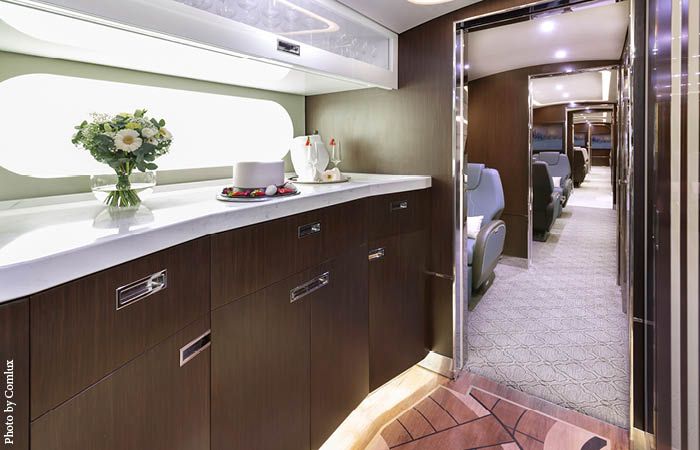
“The first aircraft was completely new and it’s a very modern aircraft, a lot of things are controlled by software,” says Richard Gaona, Comlux’s executive chairman and CEO. “When you do the first one, you’re discovering the plan and must adapt your engineering to that. Then at the end of the programme, you say what didn’t work so well, what could be better next time, and you try to integrate this improvement for the next aircraft.”
“Aircraft two was already in the facility when aircraft one was still there, so there was a lot of transfer of know-how during this programme,” Gaona continues. “It would be very, very difficult for someone who had never done a cabin like that to understand how things have been done, it’s completely modern and new – but just a learning curve.”
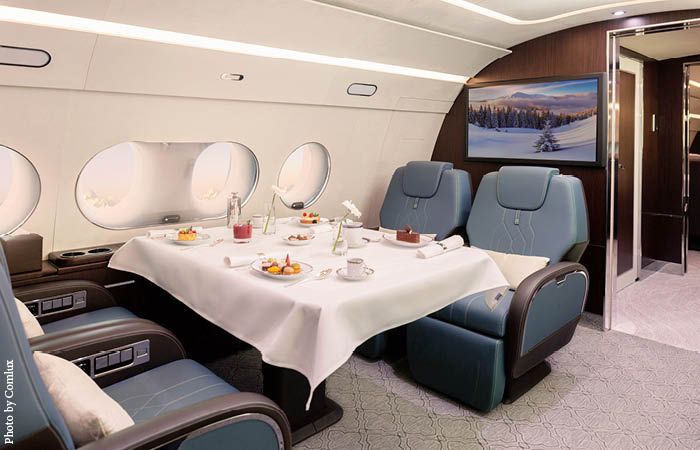
Time savings
Cabin completion is also now progressing on the third and fourth aircraft of the type, with the third due for delivery by the end of 2024. By 2025, Comlux hopes to deliver four to six of the aircraft per year, and Gaona believes timelines will condense further. “Our goal is to achieve eight months from aircraft induction to the delivery of the aircraft,” he explains. “We’re not yet there, but by repetition of the interiors we will become more and more efficient.”
“If you get three or four aircraft on a regular basis, then you can really optimise the lead time because the people are trained and they work from one plane to another,” he adds.
Gaona does caution this is dependent on the interiors sticking to the catalogue and being similar to previous ones – and this is not a sure thing because the company does work flexibly with its customers. “When you launch a programme like this, you define a strategy and you say ‘OK, the clients will be taking this and we will not do something different’,” he explains. “The reality is different. As long as this difference is not huge, or completely breaks the concept, then we try to accommodate the customer’s requests as much as we can.”
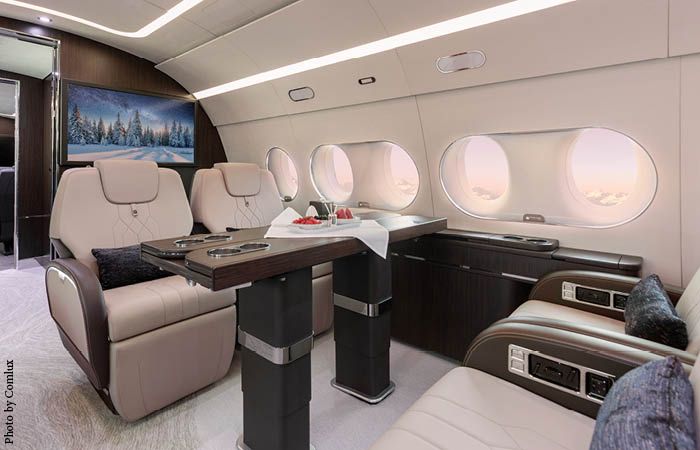
Collaboration with Airbus
Gaona says the collaboration with Airbus came about because Comlux offers not only completion centre expertise, but insights on functionality from more than 20 years as an operator. “We always use the experience of in-service aircraft to define the new one,” he says. “I think this is a strong asset we have put at the disposal of Airbus because we say, ‘This is a theory but the practice shows that we have to do it a little bit differently for operational reasons, for maintenance costs, a lot of things like that’.”
“Airbus did the artistic design of the cabin and we did all the rest – the engineering design, engineering drawings, price calculation, then production, installation and certification,” explains Gaona. “We are in regular meetings with Airbus to be sure that the product matches their expectations in terms of reference; we have a very good collaboration with them.”
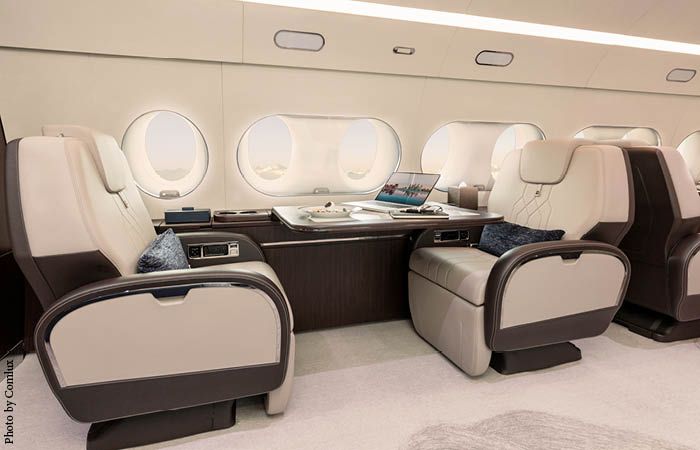
Decisions, decisions
The catalogue is not short of options – there are around 80 possible configurations, and all elements have been pre-engineered. This meant aircraft two presented no real difficulties, Gaona says.
“The table is the same in dimensions as on aircraft one, the seats are the same, and so on,” he adds. “It’s not exactly the same interior as the first one, because this time the customer is a corporation. They wanted a partition in the middle of the main cabin to have one more room. There is an additional galley in the mid cabin. In the aft bedroom, the first aircraft has a big bed, whereas this one has two face-to-face couches, which can expand to be wider during the night. Except for that I would say the rest is just a matter of colours and fabrics. This has the same kind of kitchen galley at the front, but the colour of the stone is different.”
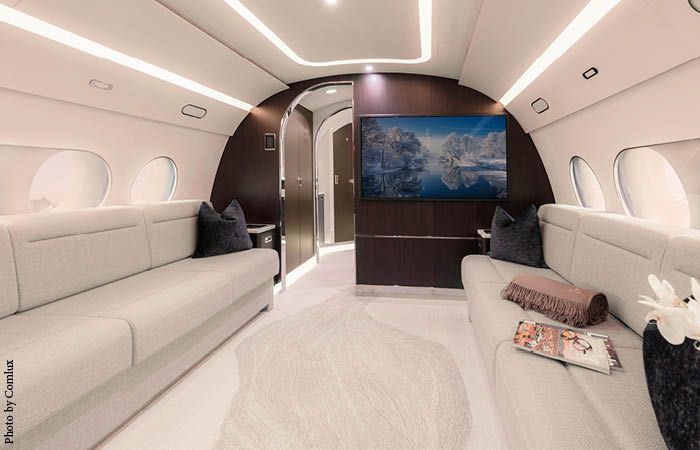
IFE and connectivity
The IFE system (from supplier CCC) and the satcom wi-fi system (from Panasonic), is “more or less the same” as on the first aircraft, Gaona shares, except for where the parts are installed. On the first aircraft, screens were installed on credenzas, not on the walls. On the second aircraft, the client wanted wall-mounted screens installed in two rooms.
Both aircraft have electrochromatic windows and inductive chargers. One difference is the second has a humidification system. A catalogue option, the system was developed by ACJ in partnership with CTT Systems and is available as a system with its own STC. The ACJ TwoTwenty humidification system is designed to increase cabin humidity up to 22% relative humidity. It’s based on evaporative cooling technology and installed along with a CTT Anti-Fuselage-Condensation system.
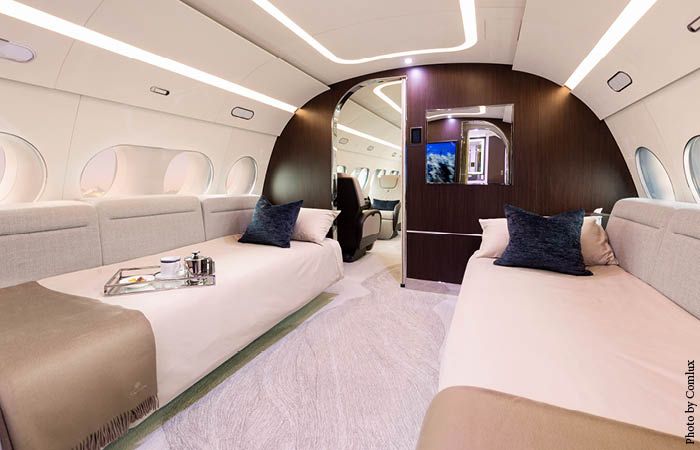
Light and sound
Both completed aircraft have full-colour spectrum LED ceiling lights. Quiet was more of a priority for the second customer, and so noise abatement was a key focus. Gaona says Comlux’s efforts on this front can include patented systems, adding insulation, sometimes between the carpet and the floor, and testing to aid in fine-tuning. However, material choices play a big role. “Aircraft one has a bedroom and then a credenza, while aircraft two has two couches done with fabrics, not leather,” he says. “The fabrics absorb noise better than something like a credenza, which is hard. We have already remarked that this room on aircraft two is quieter than on aircraft one. It’s not because we’ve been using different technology, it’s just we have a different configuration and materials. Our role is to deliver the best with what we have, and this is an example.”
This feature was written by Izzy Kington and first published in the March/April 2024 edition of Business Jet Interiors International. Read the full version here.
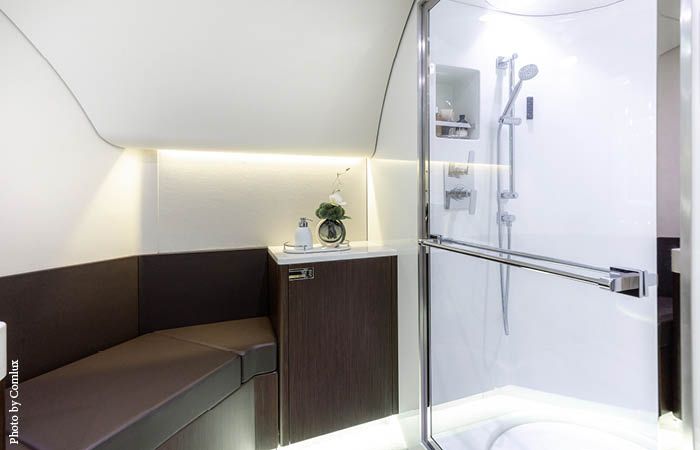