Maureen O’Keefe, senior aircraft interior designer at Bombardier, shares her thoughts on cabin material trends – from smart materials to eco-design and customisation.
Are you interested in the possibilities for smart and sustainable materials?
We are embracing environmentally minded designs that complement our ongoing research to make aviation more sustainable. Our eco-design approach focuses on offering high-end products that will allow customers to reduce their environmental footprint while maintaining high aesthetic and quality standards. Some of the initiatives implemented throughout Bombardier’s value chain include revalorising parts, recycling materials, reducing hazardous chemicals, leveraging circular economy strategies and using the latest environmentally sustainable technologies.
Concrete examples of our eco-design vision can be found in the cabin interior of the Bombardier Challenger 3500. These include bio-sourced material; rapidly renewable eucalyptus hardwood veneer; upcycled wool for seat cover options; natural and more locally sourced fibres and blends for carpet options; and more.
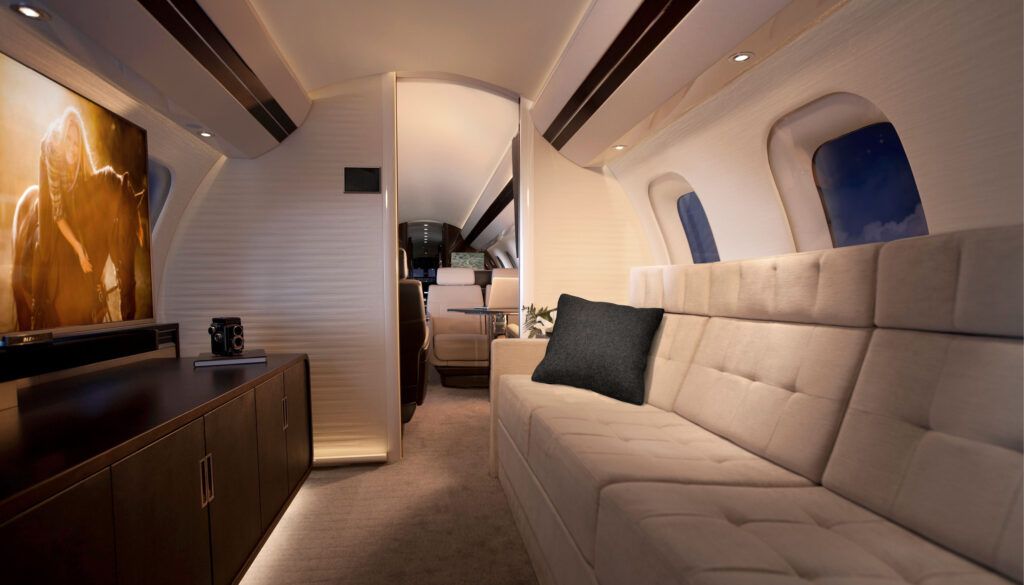
What material innovations are you most excited about?
We’re interested in smart materials that can respond and ultimately change based on evolving conditions. This can also apply to influences (i.e. an electric charge passing through them) directed at the materials. Think of cooling sheets, or clothing that adapts to changing temperatures, keeping the wearer either warm or cool, or changing colour based on the temperature. Materials whose properties can change in a controlled fashion based on external stimuli.
What should suppliers prioritise for R&D?
Bombardier’s interior design team works with many other (multidisciplinary) teams in its design concepts, including the industrial design team. They are constantly finding and testing new materials alongside our suppliers to bring new items to the table. We also work very closely with our suppliers on sustainability concepts.
Can you share a recent standout material solution?
Recent customisations have included integrated wireless charging solutions; open grain finish on veneers; and fibre optics lighting solutions integrated into materials.
How can suppliers best support customisation?
Being open to thinking outside of the box. With the restrictions that are inherent to the aviation industry (flammability, weight, etc.), it’s important for our suppliers to work with us to find solutions to those requests that may seem impossible to achieve. We also work with suppliers to collectively become more agile and flexible in the definition and implementation of custom, sustainable solutions. The key is to bridge the gap between suppliers and the designers who are offering their products by improving communication on quality, costs and changes. It’s truly a collaboration between the supplier and designer to come up with viable solutions when we are asked to customise a certain design element or treatment in the cabin.
This interview was conducted by Izzy Kington and first published in the September/October 2024 edition of Business Jet Interiors International as part of the Design Forum feature.