Various factors must be balanced to create a serene, quiet environment in a business jet cabin – including the design of the airframe itself, weight and interior materials.
Minimising noise in a business jet cabin begins with the design of the airframe itself. For example, Matthew Nicholls, senior advisor of PR and communications at Bombardier, outlines several features of the Global 7500 that were designed with this as one factor in mind. To achieve “extremely low noise levels”, says Nicholls, Bombardier has “focused attention on aircraft and engine design and noise propagation paths”.
“The aerodynamic sculpting of the fuselage minimises shockwaves, reducing sound levels, while vibro-acoustic materials are strategically layered for further sound suppression,” says Nicholls.
Wing design is also key, he says. All Bombardier Global aircraft are designed with high wing loading and high wing flexibility to provide a smooth ride. “This means the aircraft is better able to ride turbulence, providing a smooth ride, with less noticeable bumps in the cabin, and, as such, less potential rattling,” explains Nicholls.
The new environmental control system (ECS) on the Global 7500 also eliminates the need for gaspers, he says, “although the option remains for those who want them – reducing overall cabin sound levels”.
Additionally, engines are purposely placed well aft of the pressurised vessel, further from the passengers in the cabin, with the aim of reducing noise. This positioning also allows passengers baggage access at all times in flight.
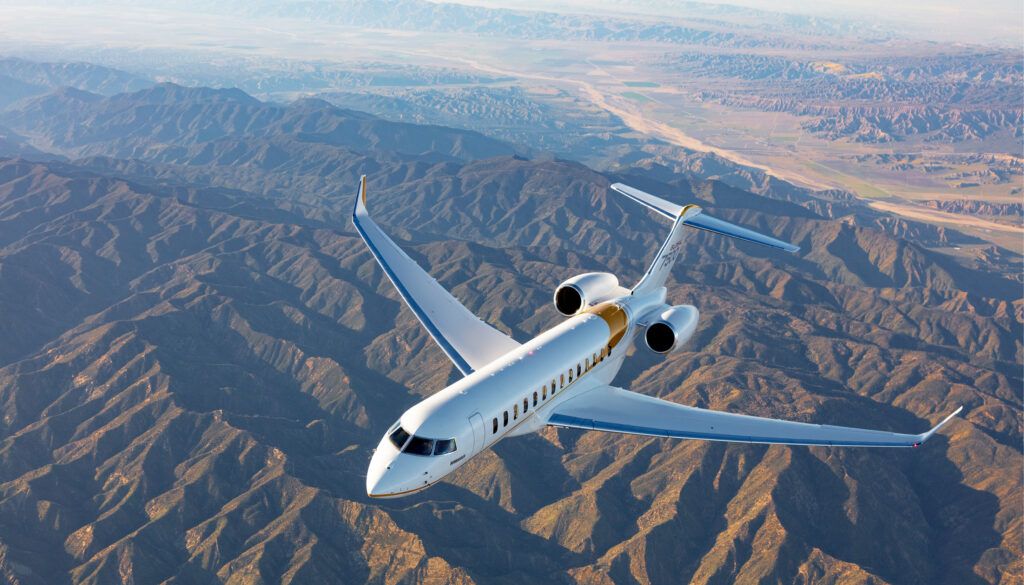
Know your airframe
For interior completion/modification centres, the airframe they are working on influences their work to minimise cabin noise. “Each aircraft type has a different acoustic profile,” says Christoph Fondalinski, VP of completions at Jet Aviation. “For example, previous-generation aircraft with an aluminium fuselage and new-generation composite aircraft fuselage have different acoustic signatures. To understand this, we also need to factor in the evolution of the systems within those generations. As such, it requires a very thorough understanding of their specificities.”
Grayson Steding, director of client support at Greenpoint Technologies, adds: “Aircraft constructed from composite materials generally produce less noise compared with those made from aluminium.”
Stéphane Bibler, senior project manager at AMAC Aerospace, also points out that, “the bigger the windows, the noisier the cabin will be”.
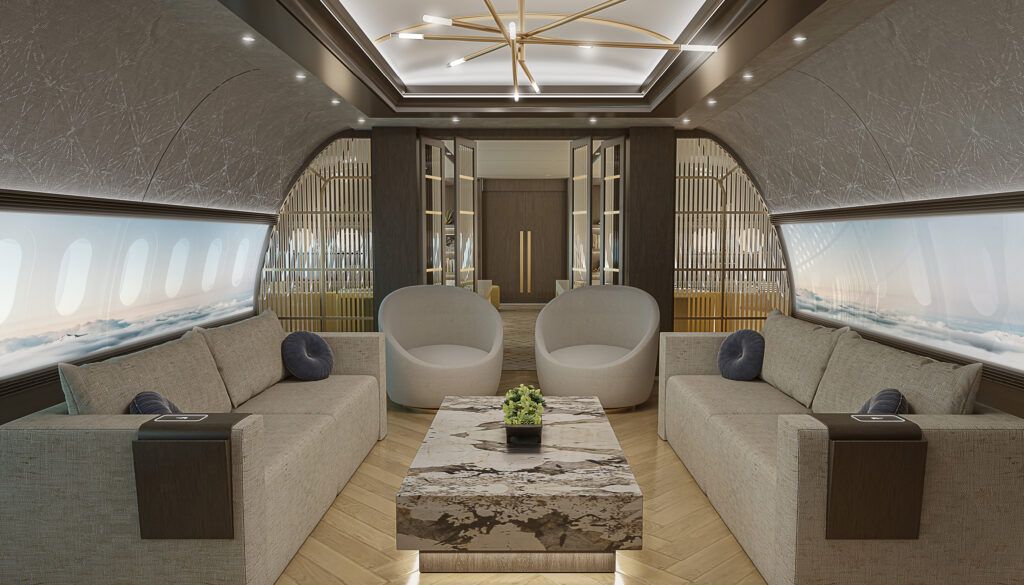
Floorplan factors
Completion centres are of course not able to change engine placement as OEMs can, but they can organise the cabin floorplan intelligently to minimise passengers’ experience of noise. Steding of Greenpoint Technologies suggests designers consider developing the floorplan around the ECS or adding room partitions to act as sound barriers. “Interior designers must understand and carefully consider the trade-offs to effectively manage and optimise acoustic performance,” he notes.
Jet Aviation has collaborated with Gulfstream to develop analytical models to predict cabin noise with different simulated interior configurations. “This deep understanding of acoustic behaviour means that we can accurately predict acoustic performance before production,” explains Fondalinski.
The idea is that by modelling how different materials and designs affect sound levels, these teams can make informed decisions before manufacturing begins.
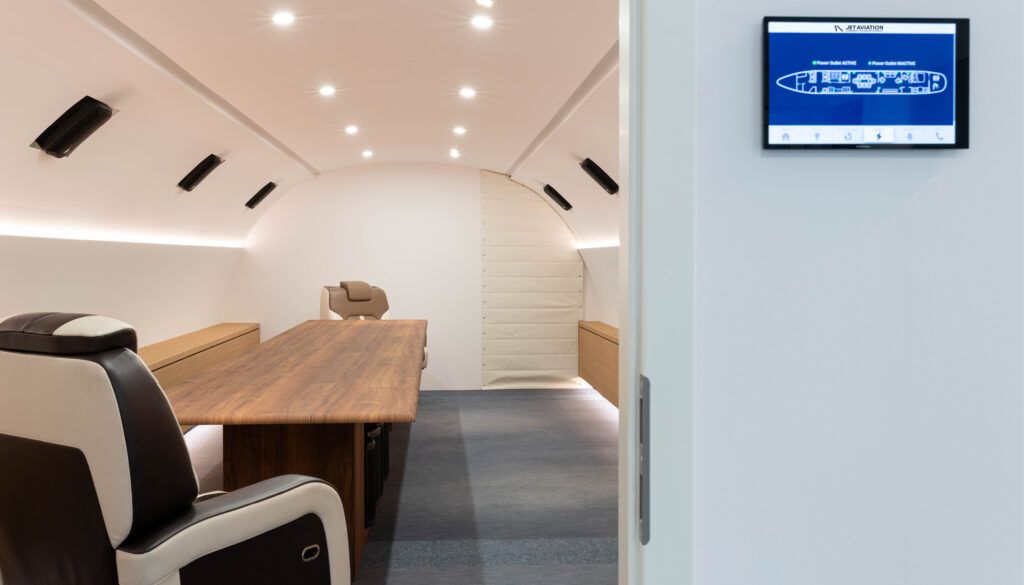
Adam White, CEO of Comlux Completion, explains more about the role of liners. “All cabin items must be acoustically isolated from the vibrations of the aircraft,” he says. “When you talk about liners, it is important that the splits are offset from the acoustic materials to ensure the noise doesn’t have a direct path to the cabin. Pocket doors or curtains are installed in-between living areas so rather than isolating airframe noise, they are used to separate noise from work areas – like the galley – to the rest of the aircraft or for privacy.”
There is also a focus on perfecting the quality of the cabin installation itself. “Rattling, for example, is not something we would expect with high-end furniture or vehicles, so we set the same standards for our aircraft,” explains Nicholls at Bombardier.
Bibler of AMAC Aerospace notes: “The fixations of the panels with grommets and specially designed air distribution also highly contribute to having quiet cabins.”
On one A319 project it could share, AMAC Aerospace’s team achieved sound levels slightly below 45dB in the bedroom by working to minimise gaps, developing a specific soundproofing package, and employing proprietary add-ons.
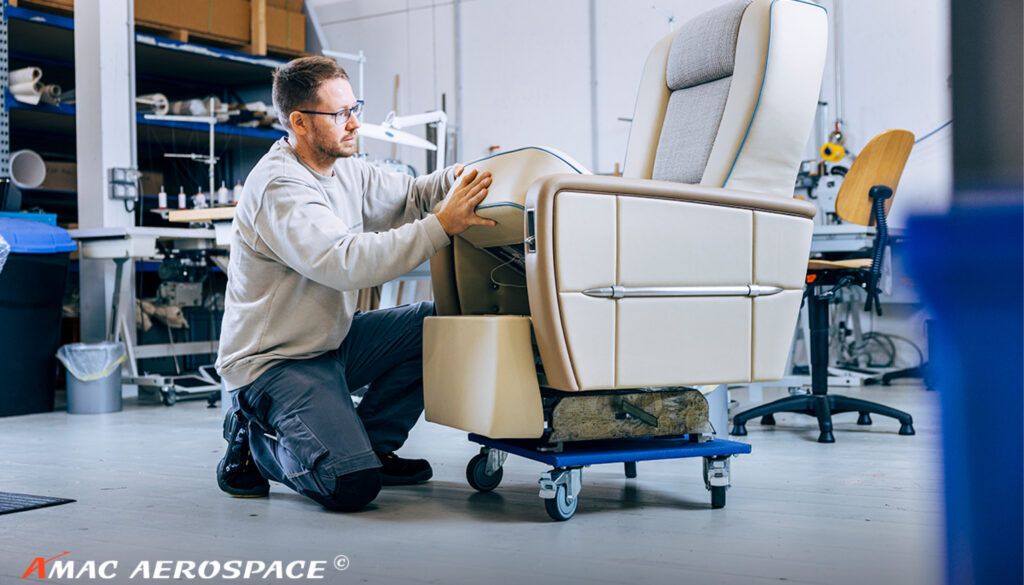
Quiet versus weight
Of course, the installation of soundproofing/dampening materials is very important in the war against noise, but here there is a balancing act to make. Bibler of AMAC Aerospace explains the most significant challenge is dampening noise without adding excess weight to the aircraft, which would impact its range and fuel efficiency. “Usually customers want very light aircraft that are also very quiet, which is contradictory,” he says.
“To redeliver an aircraft that is not only light, but also exceptionally quiet, is a fantastic achievement,” says Fondalinski of Jet Aviation. He credits Jet Aviation’s understanding of acoustics for achieving an optimal balance of low weight and noise levels on a VIP Boeing 787. The company shares it has also attained average decibel noise levels in the lower 40s in a narrowbody.
“We have spent almost a decade working on research and development to enable us to identify the exact source of a sound so that we can apply soundproofing materials with incredible accuracy,” says Fondalinski. “This means we are only applying this weight where absolutely necessary, and in the exact amount necessary, allowing us to achieve the best balance between weight and sound.”
White says Comlux Completion usually measures success based on room averages, “Mid to low 40s should be the decibel expectation for the individual points where passengers spend most of their time,” he says. “Mid to upper 40s for a room average in the customer main areas is also typical.”
Even the most advanced materials can fail to perform if not installed correctly. “The best technology for sound insulation has always been the quality of the installation,” says White. “Any open holes or ‘leaks’ will be devastating to the values you are able to achieve.”
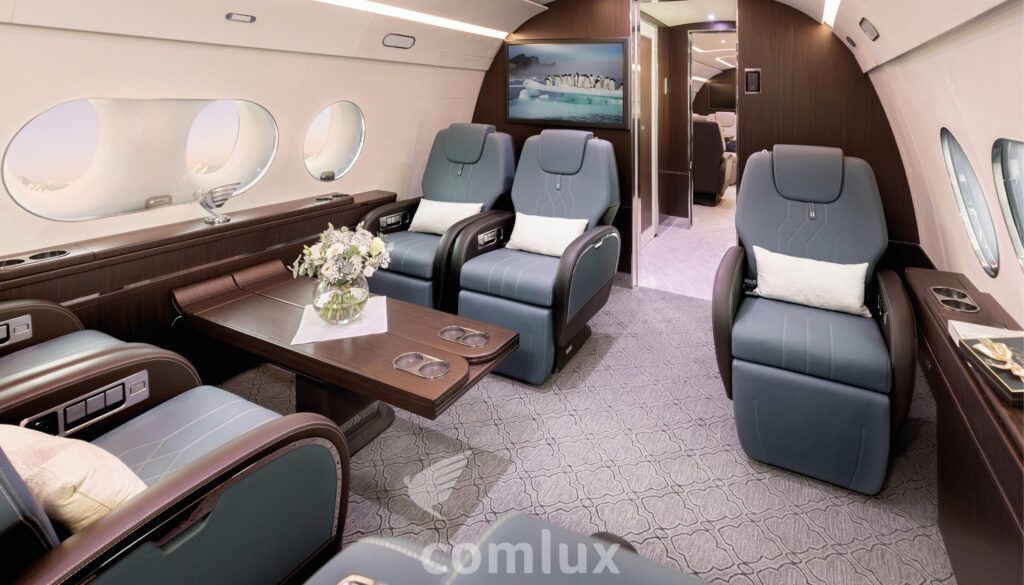
Interior materials
The choice of interior materials also plays a crucial role in noise reduction. “Soft and furry materials like padded fabrics or thick carpets are absorbing noise,” says Bibler of AMAC Aerospace. “Hard materials like stone, painted surfaces or sharp corners are not the best choice if you want to have a quiet aircraft.”
Understanding the acoustic properties of different materials allows interior designers to make strategic choices. “Interior design choices have a significant impact on sound levels,” says Steding at Greenpoint Technologies. While soft materials absorb sound, hard surfaces reflect sound waves and amplify noise in the cabin. Hard surfaces can also resonate, transferring structural vibrations into soundwaves and increasing noise in the cabin.
“Even on the seats, which have historically only used leather coverings, we are seeing more cloth-type finishes, which help reduce sound levels, while retaining the comfort,” adds Nicholls of Bombardier. “In addition, we have seat insulation and noise-dampening material around forward-facing seats in the Club Suite on the Global 7500 aircraft.”
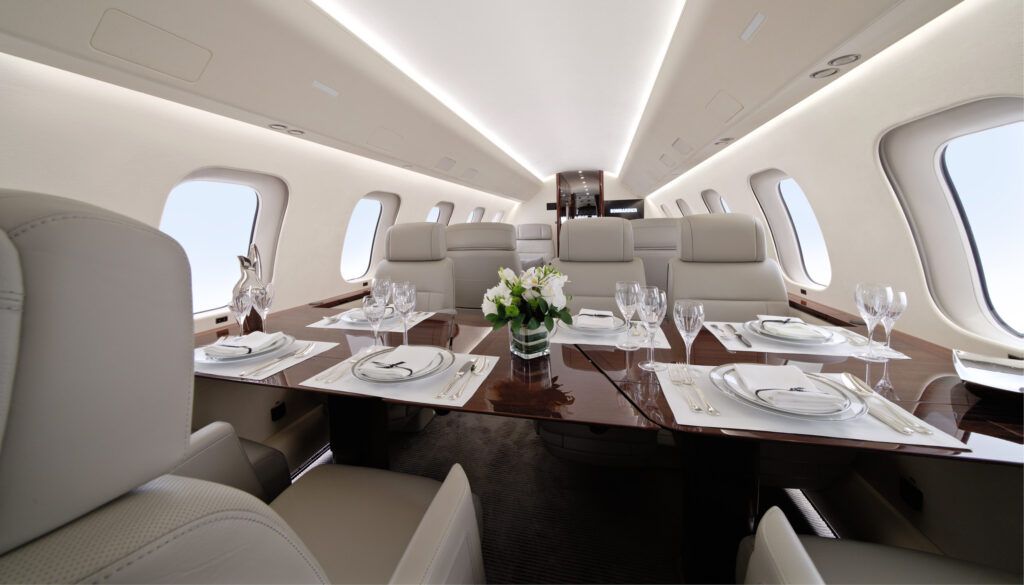
Balancing act
Navigating the balance of all these different factors is challenging. “One major challenge is managing the diverse variables and sources of noise on an aircraft,” says Steding of Greenpoint Technologies. “Addressing one source of noise may reduce the overall decibel level, but it may inadvertently accentuate other noises, creating new issues. For example, reducing loud aerodynamic and engine noise near the wings might cause the fuel pumps in the centre tank to be more noticeable, which could be more bothersome to clients. Therefore, it is crucial to approach acoustic treatment holistically and balance the extent of treatment with considerations to cost, lead time and additional weight.”
The industry is poised to continue innovating in the field of noise reduction. Fondalinski of Jet Aviation notes, “We are exploring additional technologies such as active noise cancelling in dedicated areas.”
Bibler of AMAC Aerospace also speculates that “electrical aeroplanes might be the next big step” in achieving noise reduction. White from Comlux Completion emphasises the importance of continual improvement: “The best solution and lowest values are achieved by the companies with the highest attention to detail on the installation.”
This focus on precision and quality will undoubtedly drive future innovations in cabin sound.
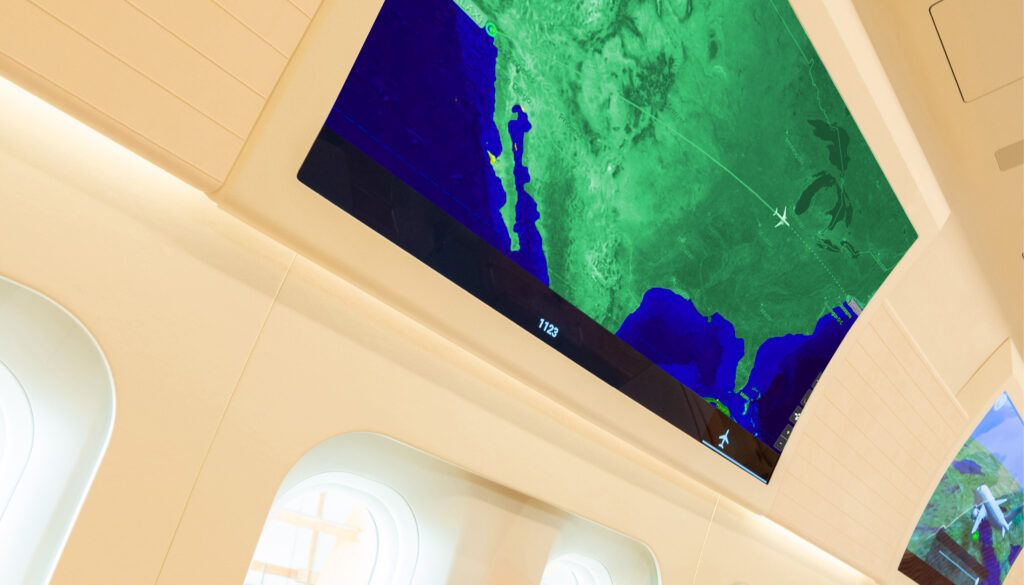
This feature was written by Marisa Garcia and first published in the September/October 2024 edition of Business Jet Interiors International. Click here for the full version.