Inspired to bring together the aviation, marine and automotive worlds, a team of experts has created a BBJ Max 7 design with flexible features including a unique champagne bar.
Despite living on different continents, designer Alexander Craker and Tom Chatfield (CEO of completion management company Camber Aviation Management) have worked on concepts together before. Recently a new one bloomed over a shared appreciation of Rolls-Royce’s Boat Tail cabriolet car, in the complementary environment of a bar designed by Riva, a boat manufacturer.
Chatfield characterises the Boat Tail as a “not very practical” but “audacious” design with a back portion that “looks like a Riva boat”, with contrasting dark and light woods. The trunk folds open to reveal a built-in picnic suite and umbrella, which Chatfield envisages being used to enjoy champagne and caviar at a polo match for example. The team was inspired by the look of the wood, and the idea of bringing people together. They wanted to create something that would be very practical in a private jet.
Unlike the team’s other projects, which normally start with functional considerations like range, weight, passenger numbers and mission types in mind, this one began as a pure styling exercise. “That allowed us to throw out the normal conventions for layouts, and we came up with something really unique,” says Craker.
As the project progressed it attracted a client who was looking for a larger aircraft. The design was developed for the BBJ Max 7 and discussions are underway to bring it to fruition. Chatfield envisages the aircraft flying to meet guests or business partners, and hosting them on board, so the client need not even disembark.
The floorplan meets the client’s needs through its flexibility. Chatfield adds that the unconventional layout is much lighter than a classic one, helping with range: “We project that it’s well underneath what Boeing suggests as a cabin weight allocation.”

Flexible layout
There’s a relatively typical entry area at the front, followed by a flexible area for children or staff, which can also be set up as a dining area with tables that stow away. There are four club seats and a large couch.
Then there’s a champagne bar with seating for three. This also has a hi-lo monitor, and the individual seats can track and swivel around for theatre-style viewing.
“Alexander has done a really interesting job by burrowing an ice/bottle holder in the bar, with a very interesting cover that allows glasses to be stowed in it,” says Chatfield. “I’ve never seen anything like that before, only something static. It’s a reveal; when you have guests on board, you can open it up and have a glass of champagne, and it then disappears and you can bring a screen up or just leave it as a flat top.”
“The client absolutely loved what that did for the space,” shares Craker. “It allows the area to do different things – to be a bar, an entertainment area, a social area.”
Dining space for eight
Next is an eight-place dining table. “It’s much larger than anything either of us have seen on a narrow-body before,” says Craker. “But that was something the client really pushed because they had a requirement for a large dining area that could also be used for conferences, teleconferences and things like that.”
After the dining area there are two buffet cabinets inspired by the Boat Tail’s picnic setup. They’re used to store chinaware, glassware and silverware. Behind those are two bulkheads with rotating monitors, and behind those, a hidden galley and passenger washroom or VIP lavatory.
There follows a private area with six individual seats and a more subtle palette of light and dark blue tones. Large ‘sails’ can be implemented here to provide privacy for each seat, or removed for a more social, open layout with seats rotated accordingly. Then follows the private bedroom and bathroom.

The seat design
Rather than a more traditional seat design, where during recline the whole back shell moves with the back cushion, on this concept the back shell and armrests are a single unit that slides back, allowing the back cushion to go flat, and the armrests end up next to the head. “We’ve been in discussion with the seat manufacturers,” says Craker. “It’s using existing structures, but with minor modifications to do something completely different. This reclining mechanism is really exciting. I hope it will be a trend we’ll also see on other projects.”
CMF options are still quite open, because the team wants to select suppliers local to the completion centre, which is yet to be chosen. “We want to make sure we’re not shipping from any further than necessary,” says Craker. “The materials we’ve selected are relatively easy to procure. Even the carpet is a very simple cream; that’s so we’re not looking at an eight- or nine-month lead time for special hand-woven carpet.”
This is driven mainly by the customer, who wants to use the aircraft a lot and so requires materials that will be easy to procure for replacement, in addition to being very hard wearing and easy to repair.
The client also wanted a very quiet aircraft, influencing the decision to go for Alcantara for linings, sidewalls, ceilings and bulkheads – supporting noise absorption without the weight of additive soundproofing.
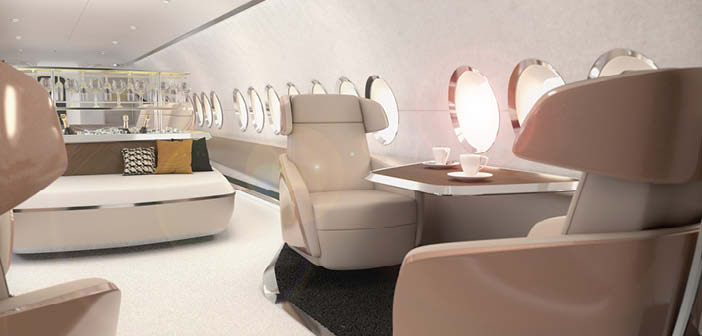
That’s a wrap
There’s not much veneer, and instead widespread use of architectural wraps/haptic foils for the seat shells, sideledges and cabinetry. “They’re applied with heat on a very flat surface, and can be wrapped around corners,” says Chatfield. “When you see supercars wrapped with a really wild design, it’s the same basic idea.”
“The wraps and foils were required because of the complicated surfaces, which we couldn’t simply veneer without increasing the costs dramatically, and it wouldn’t have helped us with that drive for a hard-wearing cabin,” says Craker. “There are lots of very complex surface treatments and compound curves. This is definitely not easy to manufacture. But on the flip side, the amount of millwork and hand finishing is greatly reduced. There was a big focus on really interesting surfacing and a lot of it was inspired by automotive and marine environments.”
The focus on combining aviation, marine and automotive influences can also be seen in the contrast of dark and light woods. “That’s what we saw on the Rolls-Royce and in the flooring of the Riva bar,” says Chatfield.

What’s next?
The client likes the concept as it stands. The next step is to flesh out the details into a high-level specification for client sign-off, then a detailed specification to form the basis of the request for quotation. “We have to define the materials and how things are built,” says Chatfield. “A specification for an aircraft like this is going to run to 180-200 pages. But we want a very, very detailed spec, so that completion centres know exactly what to deliver, which gets rid of a lot of negotiation issues. Any change to the spec is a change order, with an impact on cost and delivery. That way, a completion centre can sharpen their pencils and make a much better quote, both in terms of cost and downtime.”
Through their many contacts at completion centres and suppliers, the team has already checked the feasibility of some of the more unique elements.
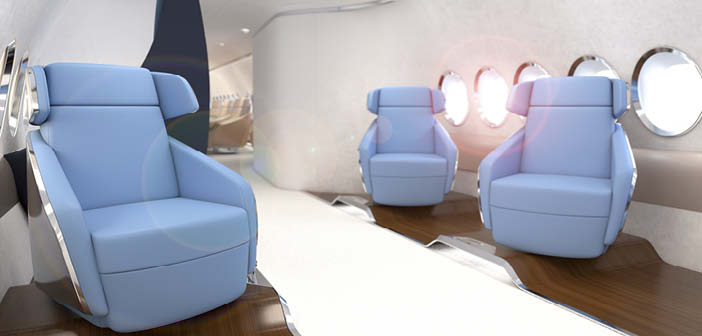
Completion challenges
Overall, it’s a simple interior and the team doesn’t anticipate particular issues with bringing it to life; although Chatfield jokes about how they might get the table in through the aircraft door!
Craker notes that such a clean design comes with one inherent, unavoidable challenge – perfection becomes even more critical than usual. “It’s very monolithic, so it does force your eyes to wander around, and if there’s any imperfections, your eye will be drawn to them immediately,” he says. “Attention to detail is absolutely critical.”
This feature was first published in the March/April 2023 edition of Business Jet Interiors International. For the full article click here.