As part of the Sustainability Drive series, VIP aircraft interior designers were challenged to create seat concepts that tackle sustainability – either showcasing current possibilities or taking a bigger leap into the future
Cosmos by Airbus Corporate Jets
Sylvain Mariat, head of ACJ Creative Design & Concepts, shares that this VIP aircraft seat illustrates what the Airbus team imagines is coming down the line in terms of technologies and new materials.
“First of all, we wanted to highlight the ergonomic aspect, a subject that has concerned us for years at ACJ,” he says.
This concept envisages the use of smart electro-active materials – as also imagined for the aircraft wings of the future – and shape-memory materials that would morph to cradle the occupant’s form.
“Thanks to this system, it would be possible to memorise the body and adapt as soon as the person sits on the seat,” says Mariat. “We also intend to recover the passenger’s heat, store it and return it if necessary. Passenger comfort has never been so central to design concerns.”
The ACJ team intends for the seat’s functions to be achieved while keeping weight to a minimum by using the latest materials, supporting reduced fuel burn. “ACJ is already working with suppliers of multifunctional and innovative sandwich composite materials that could replace traditional materials,” says Mariat. “The use of these new materials in aircraft reduces costs and weight, which translates into lower fuel consumption and CO² emissions.”
Rocking seat by Comlux Creatives and KiPcreating
This seat concept from Comlux Creatives and KiPcreating has the ability to rock back, and when reclined, the contoured seat is designed to become more like a cradle. There are accent lights on the headrest and down the arms. Additional features include essential oil diffusion from the headrest area, and a holographic display screen that projects from the armrest. These were included to ensure a VIP experience – customer experience and comfort were treated as equally important as sustainability in the design.
“Sustainable design refers to the process of creating solutions that prioritise environmental responsibility and social impact,” says Paige Pittman, interior designer at Comlux. “With the sole purpose of sustainability being this project’s requirement, our team felt that the conceptual features and design elements that make this seat sustainable should not only be incorporated conceptually but incorporated in each design moving forward.”
With this design Comlux Creatives and KiPcreating collaborated entirely towards a seat designed to be not only sustainable but also feasible with aircraft conformance. “We can ensure the use of sustainably sourced leather will endure wear over time, and repair efficiently,” says Pittman. “This extends the lifespan of the seat and reduces overall waste.”
The seat features a reclaimed veneer on the base and back shell. The team says using repurposed wood that would otherwise be discarded requires less energy and resources than producing new veneer. Weight is another factor taken into consideration throughout the design of this seat. “We aim to use printed parts throughout to attain a lighter seat overall, directly affecting fuel consumption and emissions,” says Pittman.
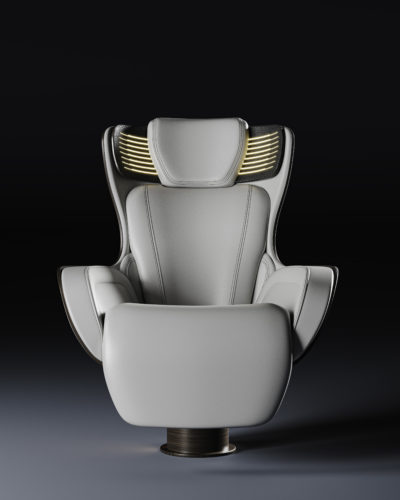
Re:Frame by NewTerritory
Re:Frame was designed by NewTerritory to ensure actionable processes that steward the product’s cradle-to-cradle approach, while radically reducing weight, waste and complexity through an agile and simplified architecture. It is intended for airline business class and the entourage sections of VIP airliners.
“Re:Frame echoes the simplicity and craft of furniture design while offering a flexible canvas for comfort, experiences and technologies,” says Luke Miles, founder of NewTerritory.
The base frame system offers an ultra-light seat with an “unlimited” amount of light customisation. Seat parts could be updated independently, to prevent obsolescence and eliminate waste through intuitive material recapture.
“By categorising the components into modules, greater furnishing and technological customisation is achieved, meaning the seat can be designed to a brand’s needs and aesthetic,” says Jérôme Nelet, creative lead at NewTerritory.
The skeleton of the seat is made of hemp-enforced bio plastic, intended to provide a robust but reduced structure. It would be dressed with componentry made using the same base PET material, which is both recycled and recyclable.
Traceability
Both hard and soft materials explore the breadth of technical finishes available in a mono-material palette. “This philosophy allows for traceability throughout the supply chain, helping to advocate for transparency and accountability of the materials’ origin and journey, and in turn improving the efficiency of the lifecycle assessment,” comments Miles.
Re:Frame is designed to be intuitive to assemble, promoting easy mid-life repair and cleaning. Upgradable modules allow the seat to adapt with evolving technology, contributing to a circular approach. At the end of the product’s life, parts would be disassembled easily and segregated into two material categories.
The challenge
“There is a cultural shift required to adapt this methodology,” says Miles. “While material innovation is scalable, it is not yet the default choice, and certification limitations may prevent growth. A new industry standard of cross-pollination is needed for the relationships required to create circular supply chains.”
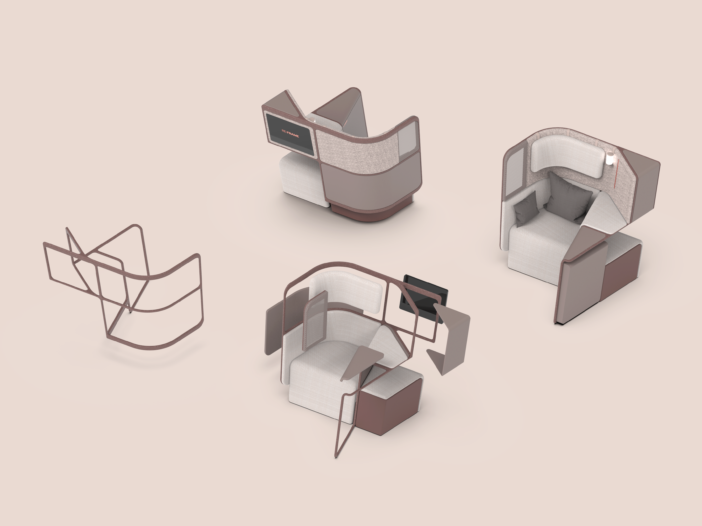
Layer Seat by Doy Design
Gary Doy, director of Doy Design, believes the luxury sector has the potential to lead the way in many areas of sustainability. “There are exciting developments in both manufacturing and materials technology that shake up the rule book and allow designers to respond to sustainable challenges in new ways,” he says. “The transportation industry is going through a transformative period and the cross-pollination of ideas between different sectors will continue to strengthen.”
Doy says next-generation seats will be much lighter, delivering greater comfort with leaner volumes that promote a greater feeling of space within the cabin. “We will celebrate topologically optimised structures within the form language and leverage additive manufacturing to deliver exciting designs that challenge tradition,” he explains.
Lightweight comfort systems using alternative cushion and cover technology will be designed to circulate back into useful products rather than going to landfill, Doy says. “Some of the new materials will be grown and harvested in more sustainable ways than before, with science and AI accelerating materials development in the very near future,” he continues. “We can also learn from nature and history to develop our sustainable designs, a return of the humble spring and tessellating geometry from nature will play a role.”
Paying attention to material combinations that work together, and designing in the separation of components at the end of life, will become common practice for new products, Doy believes.
“Extending the lifecycle and reducing weight must be significant drivers to improve the sustainability credentials of aircraft seats, especially for the next-generation of lightweight flying vehicles,” he says.
The Layer Seat would be constructed with a layering approach, to make it easier to separate its components at the end of the seat’s lifecycle
The challenges
Sustainability should be at the heart of the design process and design choices need to be informed by the emerging understanding of sustainable best practice, Doy says: “One of the challenges is transparency; we need to collect data and understand the true environmental impact of our design and operational choices to make better decisions in the future.”
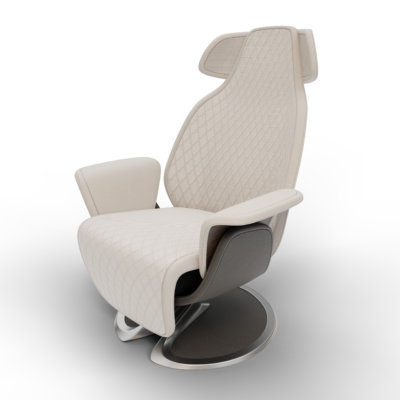
Praying Mantis by Yves Pickardt
This green VIP aircraft seat is proposed by Yves Pickardt, with the collaboration of Damien Charles. Moving towards bio-sourced materials, none of the components would come from petrochemicals or animals. Pickardt says possible leather alternatives include materials made from pineapple leaves, apple peels and mushroom mycelium: “These have a texture like traditional leather, but they are cruelty-free and have a lower environmental impact.”
Other alternatives include lab-grown leather – a meat product produced using tissue engineering techniques, avoiding the need to raise and slaughter animals, as the cells would be grown outside the animal’s body.
“Colouration would no longer be achieved by baths or the application of dyes, but by microencapsulation,” continues Pickardt. “In other words, we act at the molecular level of the material. Colours will be integrated in the form of nanoparticles. It will even be possible to modify the colours of the coatings once delivered.”
For the fabrics, Pickardt points to the “many natural and environmentally friendly” options. “These include flame-retardant water-based solutions with a neutral pH and no harmful compounds,” he says. “Meanwhile foams derived from petroleum products will be replaced by new alternatives based on soya and aloe vera.”
Pickardt believes that carbon fibres, made from chemical precursors (synthetic fibres, coal or petroleum pitch) and mainly polyacrylonitrile (PAN), will be outlawed. “Alternatives do exist,” he says. “By optimising the mechanical properties of flax fibres, for example, it has been possible to manufacture a seat with the required strength and rigidity, but with a carbon footprint 75% smaller than its carbon fibre counterpart.”
As far as metals are concerned, he’s banking on the emergence of new alloys, but for the time being will continue to favour aluminium. “It’s environmentally friendly,” says Pickardt. “It’s the most abundant metal produced by Mother Nature, accounting for around 8%
of the mass of materials on the planet’s solid surface.”
Sensor-based adaptations
Comfort is to be ensured by a thin layer of intelligent sensors with predictive capabilities to anticipate the user’s movements and adapt the seat to different morphologies. “We can also imagine the foam layer and the exterior trim as a single material, heat-moulded and tinted in the mass,” says Pickardt.
Other features include integrated speakers; thermal regulation; personal smartphone or voice control; integrated storage; and a massage function with differentiated zones.
“Of course, the seat, like all eco-responsible objects, is part of a virtuous circle that extends from the manufacture of components and materials, through shaping and assembly, to the dismantling and recycling of all recoverable elements,” concludes Pickardt.
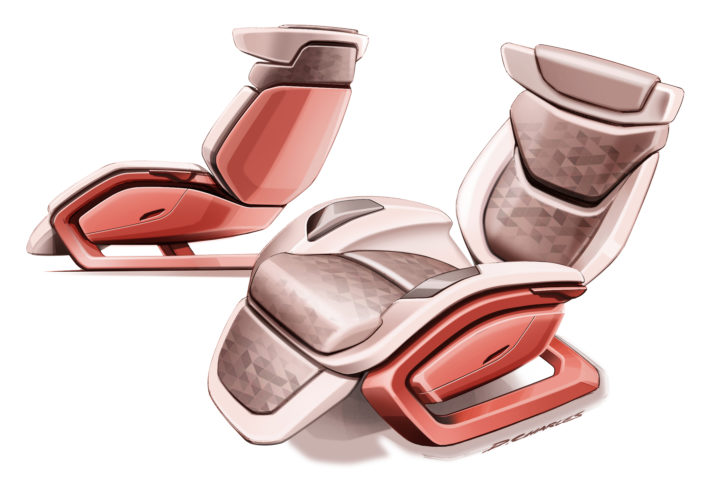
Vamp by Natalie Rodríguez Luxury Design
Vamp has a sleek profile with a composite seat frame to reduce weight and is entirely clad with the industry’s latest materials designed for sustainability.
The main textile utilised is F/List’s Whisper leather. Whisper is a vegan leather designed to be flexible, stain-resistant and lightweight at 0.75mm (0.03in) thick. Whisper is constructed from plant-based raw materials such as bio-based polymer from corn starch and FSC-certified viscose.
A glistening, jewel-like accent textile is incorporated using F/List’s Aenigma with a metallic black manta ray texture. Aenigma is handcrafted using recycled minerals from marble processing. The textile is utilised as Vamp’s inner and outer armrest inserts, in addition to low-profile accent bands in the backrest, seat pan and footrest, which are framed by a contrasting top stitch.
Golden mother-of-pearl Perroux from Siminetti’s veneers collection is incorporated as an inlay accent on the armrest, footrest and backrest, further highlighted with an integrated LED accent light on the exterior of the armrest. The veneer is sustainably sourced and at 0.3mm (0.01in) thick, designed for a light weight.
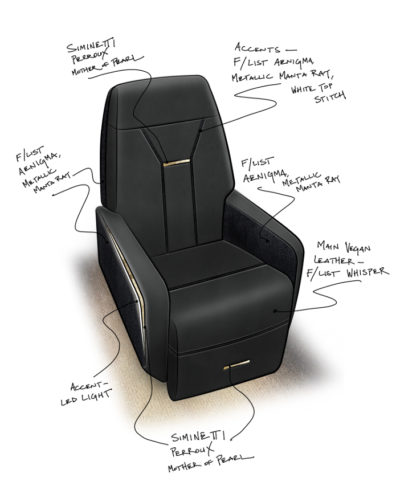
Multi-mission seat by Alexander Craker
Alexander Craker’s vision for a forward-looking seat concept is focused on reducing the carbon footprint of the production process, as well as reducing cabin weight, while increasing cabin flexibility for the client and downstream revenues for the OEM.
The aim was to reduce the number of parts needed, to keep the production process and final weight to an absolute minimum. This is achieved by using a single-piece backshell upon which the seat swivels. “The combined backrest and seat base cushion are suspended on lightweight slides and elastomeric bearings that allow the user to adjust the seat angle and tracking positions,” says Craker.
The design relies heavily on composite materials for the structural elements, as well as new developments in the areas of sustainable resin and natural fibre technologies to provide an alternative to today’s carbon fibre and epoxy. Craker notes this requires significant research and development investment to develop in line with aviation’s weight and flammability targets.
Other cabin applications
Merging the intersection between seating and cabinetry, this concept uses a common mounting system to provide additional storage and allow for multiple interior options and easy cabin reconfigurations. “This enables the client and operator to tailor the cabin for their mission and to increase the value of their asset for both charter and resale markets,” says Craker.
The concept goes beyond that of a seat, enabling the aircraft OEM to offer a wide range of interior options and upgrades. These include a three-place divan; a theatre with a 55in 4K screen and surround-sound speakers; and a dog bed and open bird cage for clients’ pets. Further options include additional storage, drink cabinets, infant cribs and more – all of which are designed to be installed easily and quickly by maintenance personnel via a service bulletin.
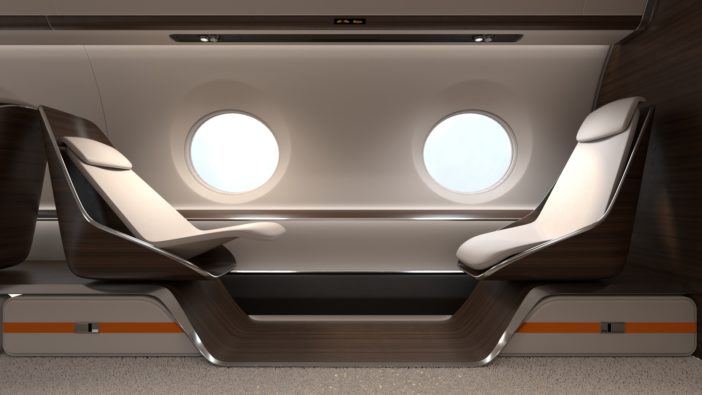
This feature was written by Izzy Kington and first published in the July 2023 edition of Business Jet Interiors International.