Experts share how seats are repaired, rejuvenated and customised as part of cabin refurbishment.
In a refurbishment project, it is more time- and cost-effective to reuse seat frames than source new seats. “New seat frames will cost two to three times more than using existing frames,” says Ben Shirazi, president at VIP Completions in the USA. “Furthermore, delivery of new seats will take six to eight weeks. So, we encourage our clients to reuse existing seat frames, unless they are planning a floorplan change. We differentiate ourselves from other shops with faster turnaround times. So, not having to wait for product lead times is a huge advantage. The main foam build-up on seats is already 80% done; we only need to do minor adjustments to accommodate new seat covers.”
In most cases at Aero-Dienst, based in Germany and Austria, only foams or covers are changed. “The advantage of reusing the structures of the seats is that we can keep costs and downtimes short,” says Mark-André Mann, team leader for interior solutions, business jets, at Aero-Dienst. “The supply of new or used business jet seats is not advantageous, takes a long time and has a significant impact on costs. The difference between seat refurbishment and replacement can be up to 500%. The main advantages of re-used seats are the costs, delivery times and, in a broader sense, sustainability.”
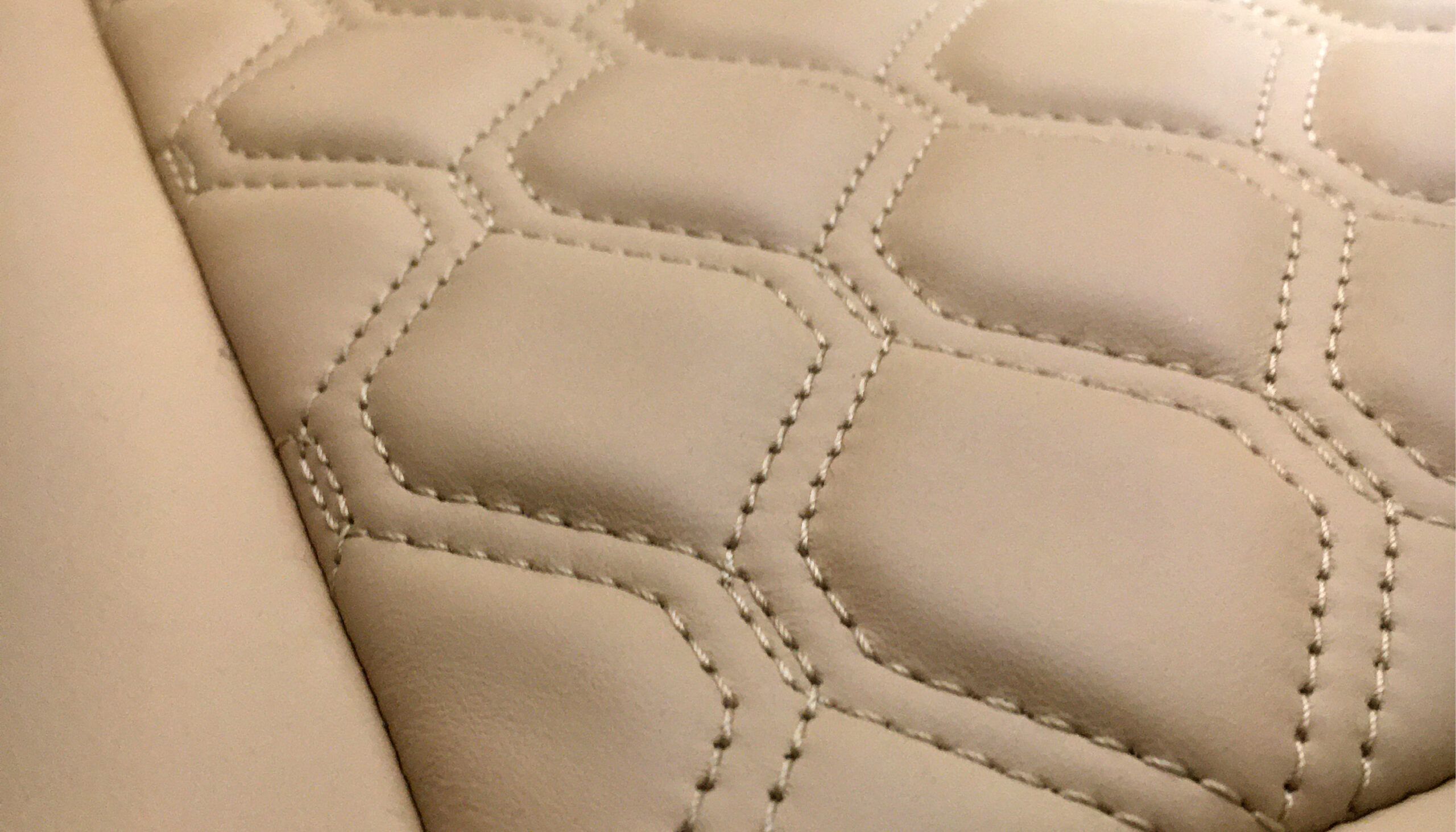
New seats are usually supplied without upholstery, Mann points out, so seat replacement incurs the cost of both the structure and upholstery, rather than just the latter for a refurbishment. “Delivery times for seat structures are more than six months, whereas leather and upholstery are available within just one month,” he says.
Aero-Dienst has built up a leather warehouse, together with suppliers, to be able to respond to short-notice customer requests. “We work with several suppliers to always find the best solution for the customer – we are constantly expanding our network to achieve this,” explains Mann.
“It’s a lot of money to buy a new seat,” agrees Bruno Chabas, cabin project manager at Dassault Aviation Business Services (DABS), a Dassault MRO based in Geneva, Switzerland. “Generally, whatever the aircraft, you won’t change seats, but you’ll change all the foam and the leather or fabric.”
The process
A seat refurbishment project begins with an inspection. “We discuss the customer’s requirements and define the optimum repair method,” says Mann of Aero-Dienst. “We show the customer various leather samples from our showroom and explain the advantages and disadvantages of each material and repair method. Once all the materials have been defined, we select the best suppliers for the job and implement the project accordingly.”
VIP Completions’ Shirazi outlines how the seat is disassembled in the seat shop once removed from the aircraft. “We separate all plated parts, which are sent to one of our approved vendors for a new customer-selected colour,” he says. “Leather covers are then removed. The foam is steamed to bring it back to its original shape and minor modifications are done to accommodate the new dress covers. We make all new patterns to ensure a perfect fit when the new leather covers are sewn. Once covers are installed, we reassemble the seat. This is when any defective parts are replaced. After the seat is completed, we reinstall it in the aircraft and do final post-installations adjustments.”
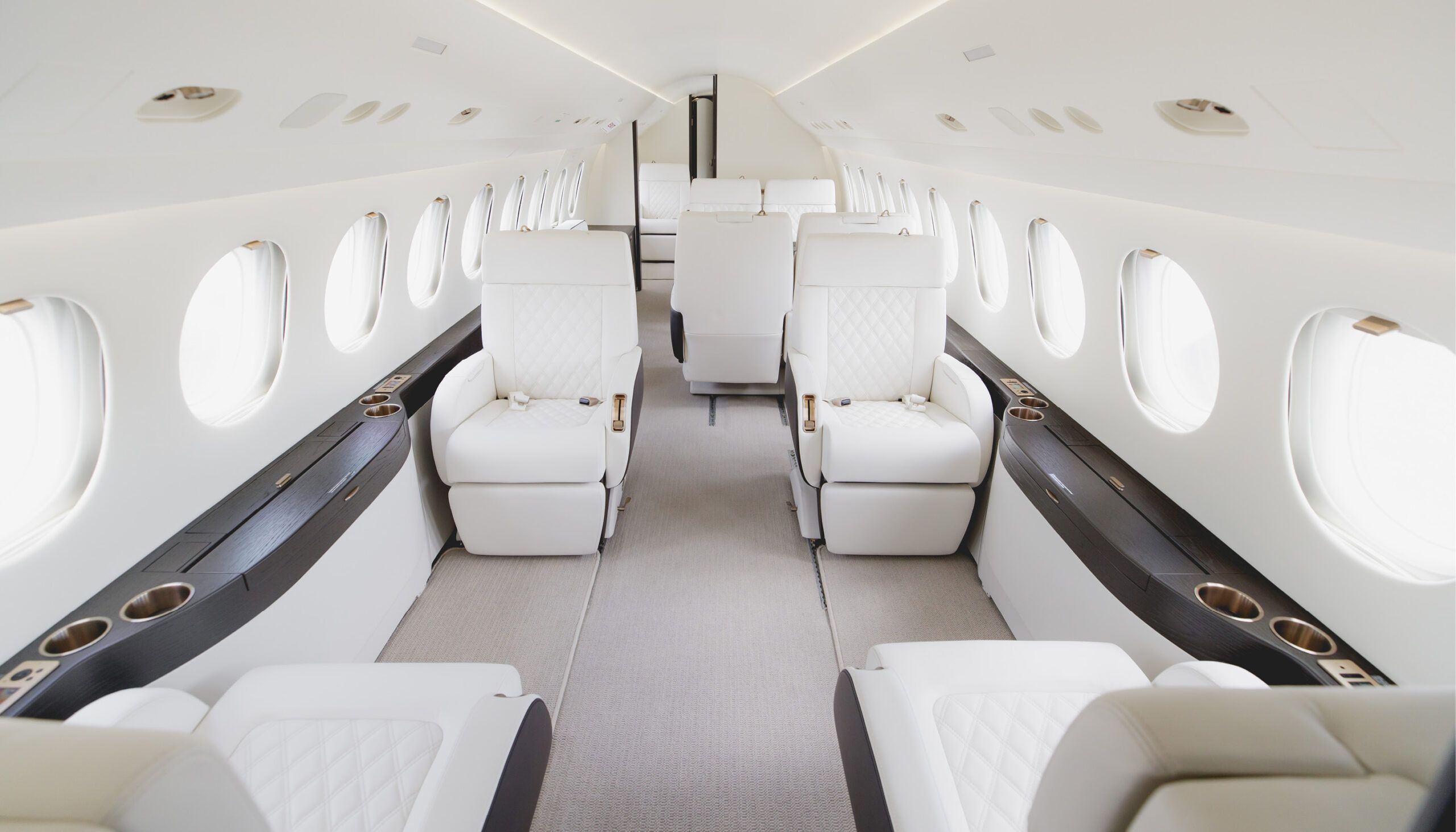
Common repairs
Shirazi says the most common defects to resolve include broken seat cables, leaking hydro locks and loose wires. One challenge of the repair route can be locating parts if a seat is from an early-model aircraft, he adds.
At Aero-Dienst, the most common requirements (on around 90% of aircraft) are simple repairs to freshen up the colour of the leather and repair worn surfaces. The second most common action is to replace seat covers, as part of a full cabin refurbishment or design change; and the third is the replacement of seat upholstery.
“The longer the seat is used, the less elastic the foam becomes and the less comfortable it is,” says Mann of Aero-Dienst. “At this point, it is advisable to replace the foam and give the seat a general overhaul.”
Chabas of DABS notes that there are limits to what can be done, as laid out in the limitation drawings from the OEM. “It’s certified to a certain weight, position, seat height,” he says.
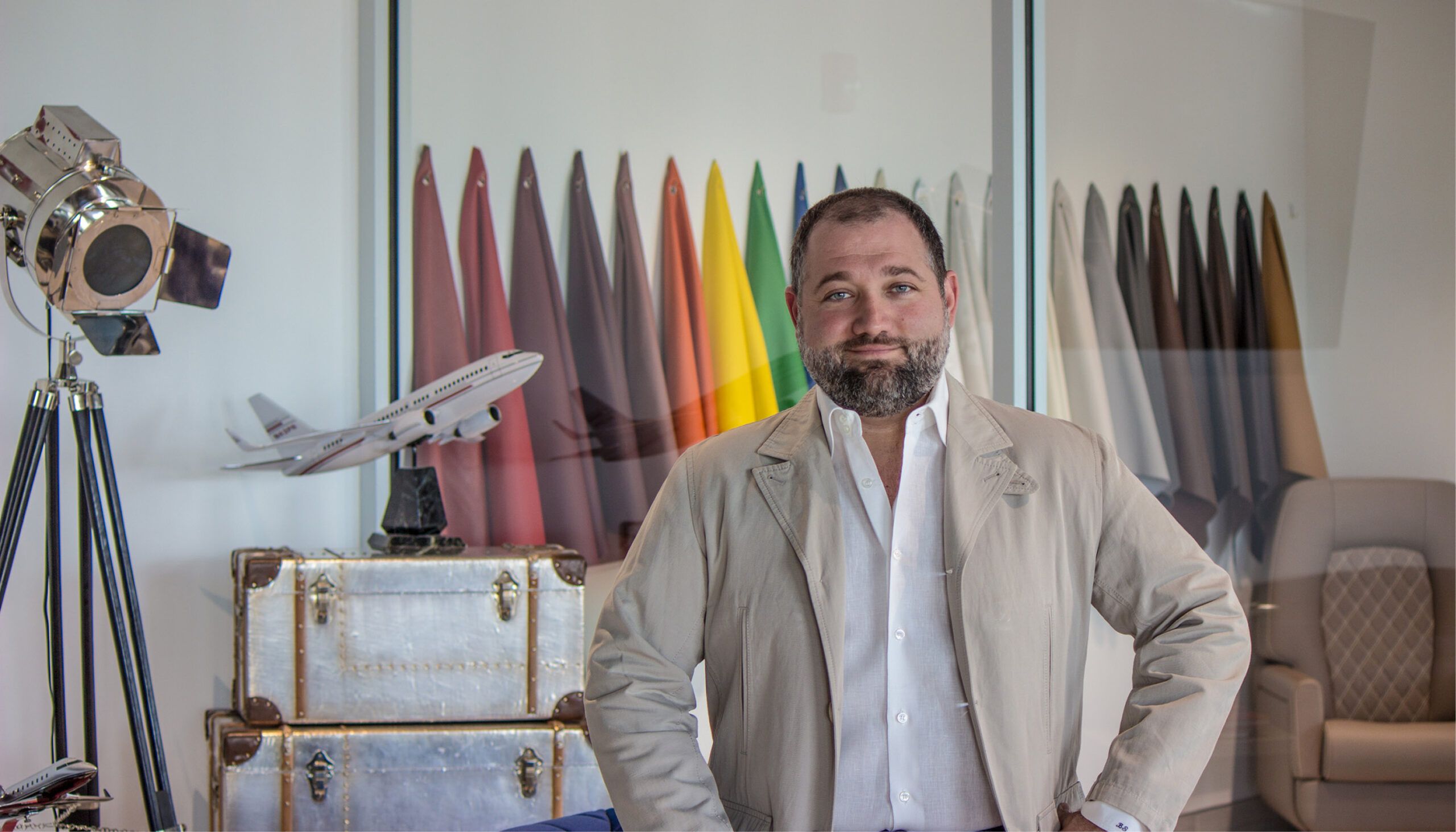
Shirazi of VIP Completions says the biggest challenge is “getting upholstery modifications approved by the substantiation report provided by engineering”.
Aero-Dienst’s Mann elaborates on fire testing requirements: “It’s very important to prove that both the individual materials and the combination of materials do not burn. Proof must be provided for each material that it fulfils the fire requirements.”
Falcon 7X programme
DABS recently launched a refurbishment programme for Decrane VIP seats on the Falcon 7X – designed to cut the cabin refurbishment downtime to five weeks (from up to 12 weeks), given the right advance notice. Many of the type are due for their 2C-Checks. “The problem is customers don’t fully anticipate what they want, which could limit what we can do later,” says Cyrille Pillet, DABS’ VP of customer support and technical services, and head of design organisation. “The more advance notice we have, the more options we can explore.”
To get a head start on production, DABS has created six designs that act akin to first articles, to showcase the leather, stitching, piping and foam firmness options. The customer cherry-picks their selections ideally two to three months ahead of the aircraft input. “We still produce a first article, but start working on the basis of the agreed specifications,” says Pillet. “About 70% can be done before the aircraft comes to base, depending on the design.”
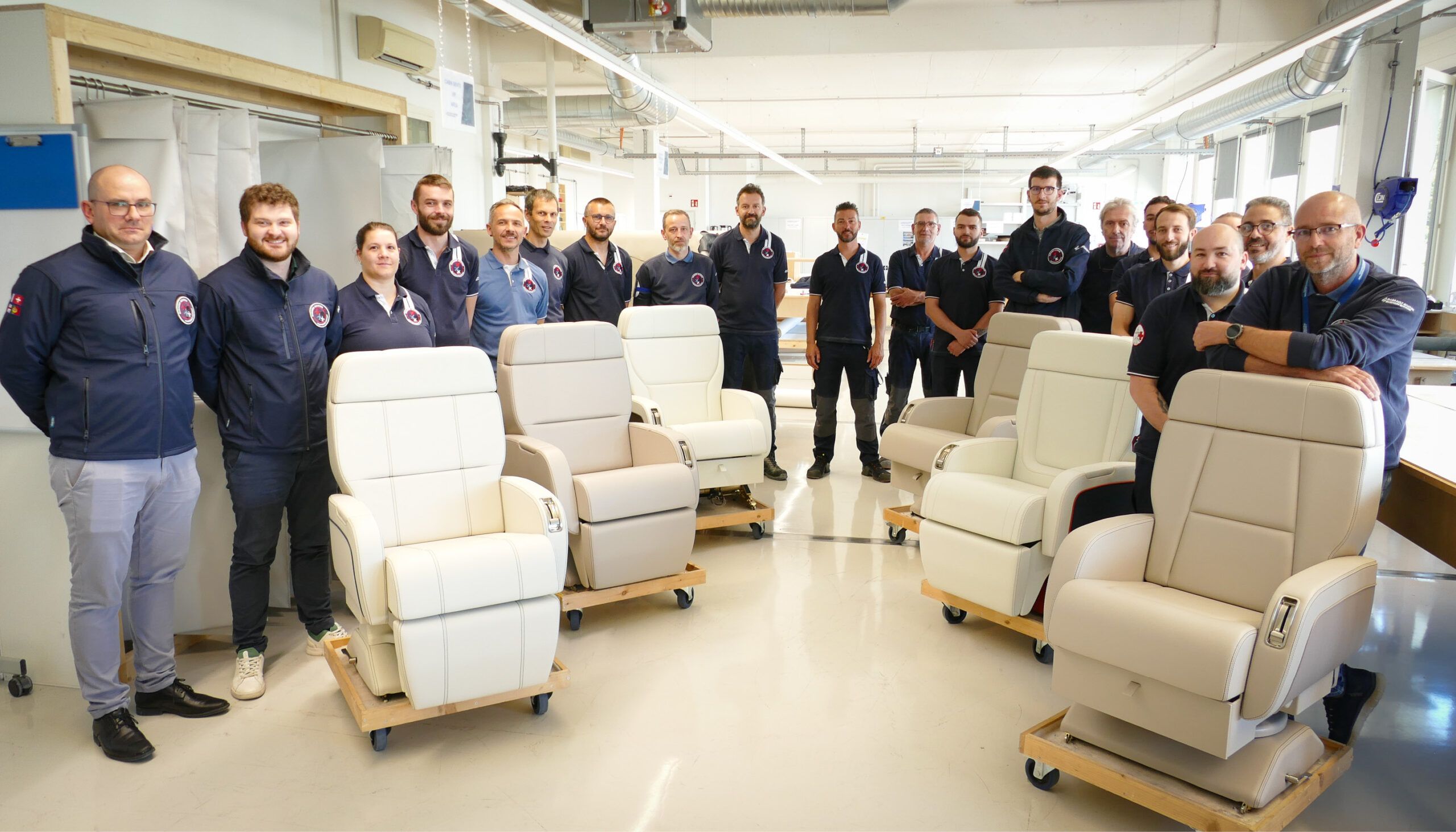
Getting ahead
The upholstery is produced without the frames, and fitted once the aircraft inputs. Armrests and legrests can’t be done in advance, due to their complexity. Getting ahead on the seats means resources can be concentrated on other things when the aircraft is on base. The length of the downtime will depend on if it’s a known design, and what the rest of the refurbishment entails. The seats still have to be burn-tested, because of the leather.
DABS can still create one-off seat designs; this new programme was developed as a shorter-downtime option to meet most people’s requirements – at least for those whose Falcon 7X sports original Decrane frames. The programme is only compatible with those. “The brand was discontinued, but two-thirds of the Falcon 7X fleet is equipped with those, and those aircraft have their 2C-Check due,” says Pillet.
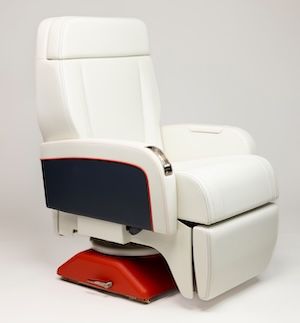
3D-formed top
DABS also used the opportunity to work on aspects of the seat design. The in-house Part 21 engineering department and cabin interior shop collaborated on a new headrest, implemented in a 3D-formed malt resin. As a Dassault-owned facility, they had easy access to the OEM specs. “We’ve developed a kit that replaces the combination of foam and glue that was used in the original design,” says Pillet. “We can not only assemble the top part faster, but also achieve a much better finish and more durability because there is a rigid structure inside.”
Now the headrest can be removed without having to cut through foam glued to the frame, it’s easier to get to the lumbar support and seatbelt mechanisms inside, DABS shares. If the seat is damaged in operation, the affected part can be accessed without removing the whole seat, which in the 7X means removing the galley, Pillet explains. “Thanks to this plug-and-play design, mechanics can get access, fix it, replace it, put it back on,” he adds.
DABS says the added cost of the 3D kit is balanced out by labour savings. It’s not charging more for this offering. “Customers get all those extra features and that’s how we want to differentiate for the same price,” says Pillet.
He adds that if the concept sparks a lot of interest, it might be developed for other frames.
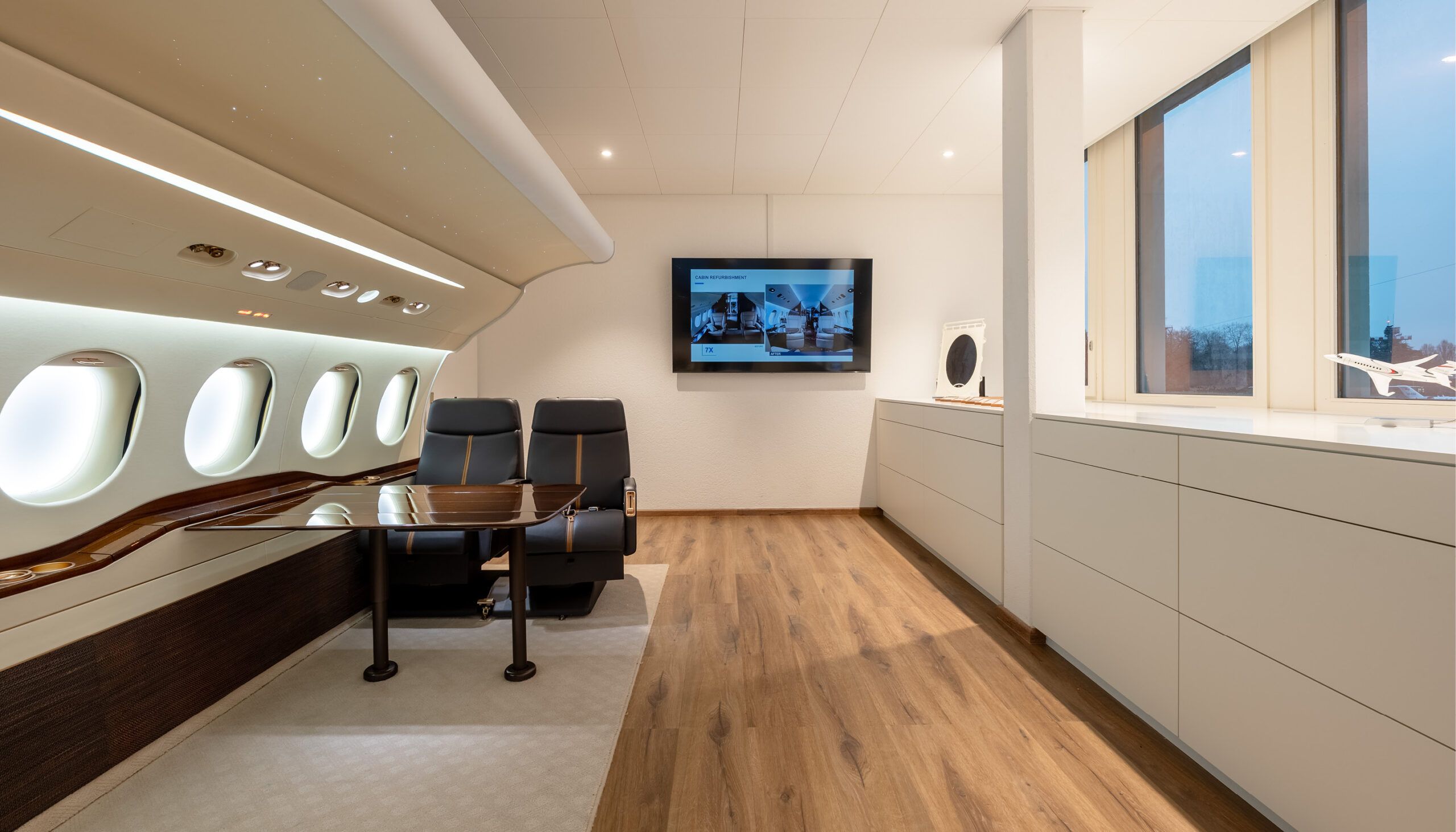
This feature was written by Izzy Kington and first published in the July 2024 edition of Business Jet Interiors International. Click here for the full version.