Jeff Lake, president of Duncan Aviation, details how the centre has responded to the challenges of the pandemic – keeping its staff safe, helping the local community and delivering socially distanced travel for its customers.
Have you been able to stay open/offer your full array of services throughout?
Duncan Aviation has been able to stay open at all of our main facilities, avionics satellite stations, and engine rapid response launch locations. Our facilities are operating at full staff, and we are staying busy meeting customer needs.
What new operational procedures have you implemented?
We have educated team members on proper hand washing, wearing masks as needed, and social distancing requirements. We have provided everyone with cloth face coverings and personal-sized anti-bacterial bottles to keep with them at all times. We have always kept clean facilities, but we have increased the frequency of cleaning and disinfection, especially for high-traffic areas. We have developed policies for self-isolation if team members present COVID-19 symptoms or are exposed to someone who has possibly contracted the virus.
We have implemented a restrictive travel policy for unnecessary travel, and we have discontinued all tours and vendor visits. Customers are encouraged to track their projects through our robust myDuncan project management tool rather than staying on-site with their aircraft. A good portion of our workers who are able to work from home are doing so.
We are also disinfecting the interiors of customer aircraft upon arrival at our main MRO facilities and again before delivery.
Developing new policies as information about the virus was still being learned and recommendations from the CDC and the local health departments were consistently changing was, of course, a challenge.
How has demand been impacted, both in terms of work volume and the type of work?
We have certainly seen business levels drop, but not as significantly as we initially feared. Some operators kept flying, some even saw an increase in their flying as they made essential trips in a smaller, safer environment for their passengers. Most did not utilise their business aircraft as much though.
Understanding that the need and desire to travel will likely increase, we believe that business aircraft will be even more valuable. Many operators moved their maintenance and aircraft projects up and got them completed so their assets would be ready when the businesses are able to use them again.
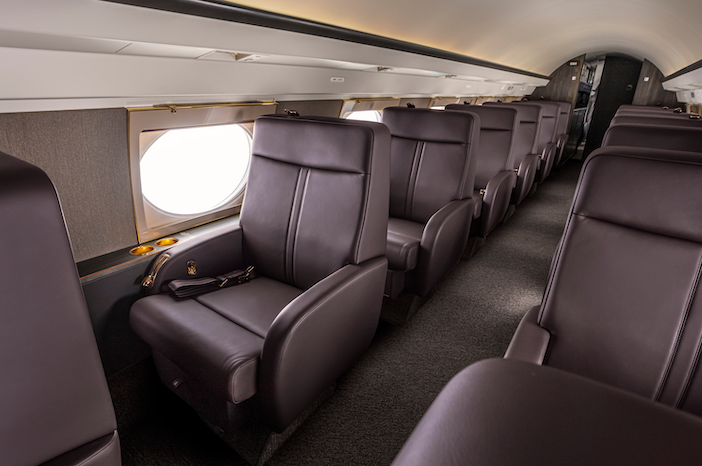
Have you adapted to make more use of technological tools?
Our existing online customer communication and project tracking portal, myDuncan, has become incredibly valuable during this time. It was developed to provide better and fast communication and to allow operators to follow their projects even if they were not able to stay with the aircraft.
Do you think there will be any long-term changes to the industry going forward?
While we don’t have a crystal ball and there are a multitude of dynamic factors that will ultimately determine how this pandemic will affect the industry, it is our belief that business aviation will hold a special spot in the recovery of our nation and the world. When the necessary travel restrictions required to fight the spread of COVID-19 are lifted, business aviation will lead us through the coming economic and societal challenges by providing necessary travel in smaller, safer environments.
Are you planning any adjustments to your operations in light of these predictions?
We are always listening to customers and responsive to their needs. We anticipate that there will be more demand for high-density aircraft interiors and other systems that will make having more people onboard more productive and pleasant – such as CMS, improved connectivity and floorplan alterations that provide room for more passengers.
Has your company been involved in community support projects?
In late March, Duncan Aviation team members had begun social distancing and we began looking to acquire face coverings for use by team members when they absolutely had to work together in close quarters, like in an aircraft flight deck, for a short period of time. It became obvious that mask supplies were depleted and that health care workers and those working directly with the public in service roles didn’t have enough to meet their anticipated needs. Our interior and upholstery teams reached out to a local hospital and asked for help in designing a mask, as well as advice on what we could do to support hospitals during this time of need.
The hospital shared specifics and two different mask templates were created. Using the hospital’s instructions, we digitised the designs for cutting with our automated fabric-cutting machine, which usually cuts leather, sheepskin and other durable materials for use in business aircraft. Depending on the width of the material used for the masks, we could cut materials for up to 900 masks every hour. To date, the company has cut more than 30,000 masks.
Sewing the masks is a bit more time-consuming. Upholstery professionals with our full-service facilities in Lincoln (Nebraska), Battle Creek (Michigan) and Provo (Utah) have been sewing masks, as have more than 300 volunteers from local churches, fabric stores and hobby groups in the communities Duncan Aviation calls home. The company has also cut and sewn hundreds of medical gowns for community health facilities.
This all started with a team of employees who recognised a problem and had the means and desire to solve it. It is indicative of the creativity, compassion and initiative found in our team members. And we are happy to help our communities in this manner. We feel it is the least we can do and appreciate the opportunity to show our concern and gratitude to those working on the front lines of this pandemic.
Check out the upcoming July 2020 issue of Business Jet Interiors International for a full report on how completion centres around the world have responded to the COVID-19 pandemic.