Jamco America has made its machine shop in Everett, Washington, available for contract aerospace projects, in addition to its use for internal product development and fabrication. The aircraft interior product supplier and integrator says the shop’s extensive machining capabilities enable it meet rapid lead times and considerable customisation requirements.
In its nearly 30 years of operation, the machine shop has expanded from basic machining to extensive equipment. Its capabilities include sheet metal bending, profiling and forming; countersinking, dimpling, riveting and other preparations for sub-assembly; large four-axis horizontal milling and machining; smaller three- and four-axis vertical machining; and lathe turning for round components. The large four-axis machine centres hold 240 tools each, and are accompanied by an automated 36 pallet cell, for flexible and efficient milling, 24/7.
In the summer of 2020, Jamco expanded the shop’s capabilities with the addition of a freeform CNC tube bender. This machine forms a round tube into a tubing frame and is used to produce Jamco’s Venture business-class seats with embedded aluminium edge trim. The shop also houses a digital cutter/router for composite materials, open cell core, textiles and more. Used traditionally in the sign-making industry, Jamco has adapted this technology for aircraft seating and other projects.
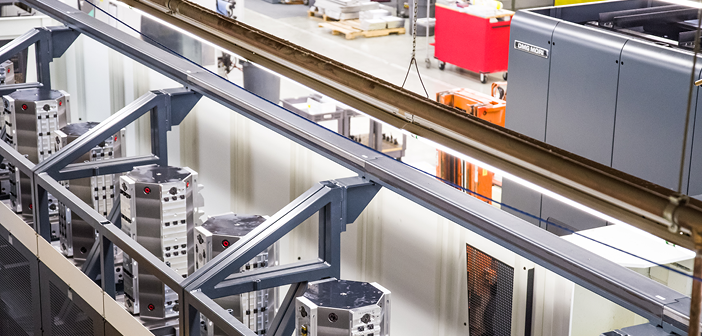